Overcoming Surface Defects in the Injection Moulding Process Step by Step
Ever seen injection-molded parts with dull spots or an “orange peel” look? These surface issues can be a big problem for makers. But, by understanding what causes them and how to fix them, you can get a perfect finish. Let’s explore the injection moulding process step by step with THY Precision and find out how to beat these common problems.
The injection moulding process step by step is quite complex. It involves the injection moulding machine, the mold design, and the plastic materials used. Each part of the moulding cycle can lead to surface issues. Things like bad mould design or temperature and pressure changes can cause problems. By knowing what causes these issues, you can make changes to your injection moulding process step by step for better results.
Key Takeaways
- Learn about common surface defects in injection moulding, like dull spots and the “orange peel” effect.
- Find out how to improve your injection moulding process step by step to fix these issues. This includes adjusting injection speed and mold temperatures.
- See how mould design and plastic materials affect the surface quality of injection moulded parts.
- Discover practical steps to get a flawless finish every time, reducing injection moulding defects and improving your injection moulding applications.
- Understand how fixing surface defects can affect the injection moulding cost. Also, learn how to use injection moulding simulation for better results.
Dull Areas on Injection Moulded Parts
The injection moulding process step by step can be tricky, especially with defects like dull areas. These flaws can ruin the look of your product. Knowing what causes them helps you fix them early.
Design-Related Causes of Dull Areas
Design issues are a big reason for dull areas on injection moulded parts. Sharp changes from the gate to the part, or sharp mold edges, can push away the resin’s cooled surface. This makes the surface look dull and uneven.
Using resins that don’t flow well can also lead to dull areas. When the resin moves through the mold, the cooled surface near the gate gets pushed away. This creates a faint, dull ring around the sprue.
Cause | Description |
---|---|
Sharp Transitions | Abrupt changes in the mold design, such as between the gate and the part, can displace the cooled surface layer, leading to dull areas. |
High-Viscosity Materials | Poorly flowing, high-viscosity resins can cause the cooled surface layer near the gate to be displaced by the melt flow, creating dull concentric rings. |
Sharp Edges | Sharp edges in the mold design can also contribute to the displacement of the cooled surface layer, resulting in dull areas downstream of these features. |
To fix these design-related causes of dull areas, make sure the mold design has smooth transitions and small radii. This keeps the surface of the injection moulded parts even and smooth.
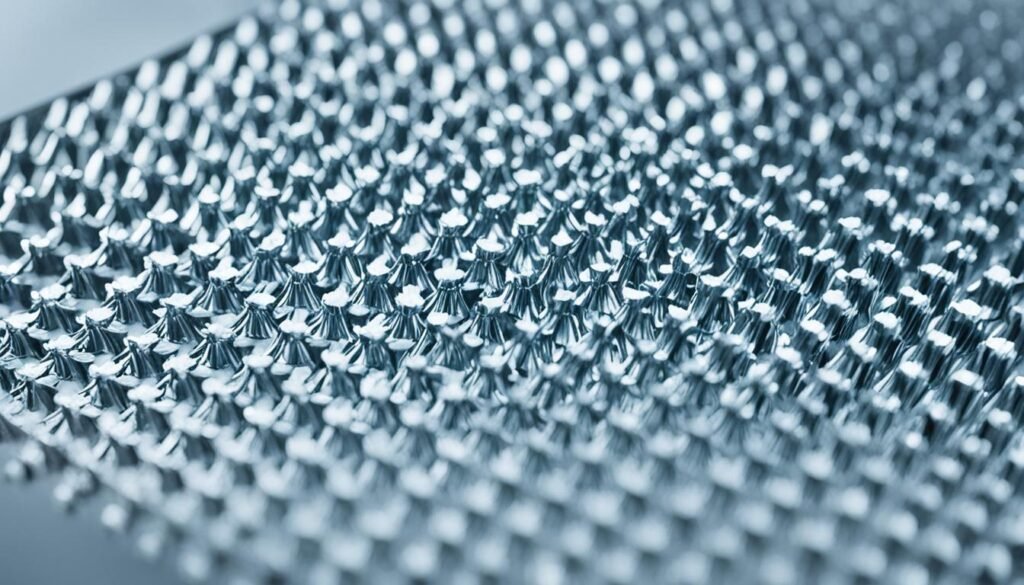
Gloss Variations on Injection Moulded Parts
Getting a consistent gloss on injection moulded parts is a big challenge. The injection moulding process step by step is key to the final gloss. Knowing what affects gloss variations helps manufacturers make products that look great.
One big factor in gloss variations is how well the mold surface is replicated. If the pressure of the melt varies as it goes through the mold, some areas might look different from others. This is especially true for areas far from the gate, where pressure is lower.
Design Factors Contributing to Gloss Variations
To lessen gloss variations, manufacturers can look at these design factors:
- Higher melt or mold temperature can make mold surface replication better and lessen gloss variations.
- Changing the holding pressure and holding time can also help with mold surface replication and gloss consistency.
- Design changes, like big wall thickness differences, can affect gloss variations.
Design Factor | Impact on Gloss Variations |
---|---|
Melt Temperature | Higher temperatures can improve mold surface replication and reduce gloss variations. |
Mold Temperature | Higher temperatures can also enhance mold surface replication and reduce gloss variations. |
Holding Pressure | Increased holding pressure can help maintain mold surface replication and minimize gloss variations. |
Holding Time | Longer holding times can contribute to better mold surface replication and more consistent gloss. |
Wall Thickness Variations | Large changes in wall thickness can lead to uneven pressure distribution and result in gloss variations. |
By understanding and working on these design factors, manufacturers can make the injection moulding process step by step better. This leads to consistently high-gloss surfaces on their parts, meeting customer expectations.
The Orange Peel Effect in Injection Moulding Process Step by Step
The “orange peel” effect is a common issue in injection moulding. It shows up as a rippled surface on parts, especially those with thick walls. High-viscosity materials are often to blame. To fix this, we need to understand why it happens and how to stop it.
When the melt is injected slowly, the outside solidifies too fast. This makes the flow uneven, leading to ripples. These ripples set before the holding pressure can fix them.
To avoid the orange peel effect, try these steps:
- Raise the melt temperature
- Increase the injection speed
These changes help the melt flow and cool evenly. This reduces the chance of a rough surface. By fine-tuning the process, manufacturers can make parts with a smooth finish.

Dealing with the orange peel effect is part of mastering injection moulding. Paying attention to factors like material viscosity, injection speed, and melt temperature is key. This way, THY Precision can always meet their clients’ high standards.
Common Injection Moulding Defects
Understanding the injection moulding process step by step is key for making high-quality parts. Even with careful attention, parts can have injection moulding defects. These can affect how the part looks and works. It’s important for manufacturers to know and fix these issues.
Flow lines are visible lines on the part’s surface. They happen when the melt flow is uneven during injection or when cooling is not even. Sink marks are depressions caused by uneven shrinkage or bad part design.
Surface delamination happens when the outer layer of the part comes off the inner layers. It’s often due to bad material choice, wrong mold design, or wrong processing. Weld lines are lines where the melt flows together. They can make the part look bad and weaken its structure.
Injection molded parts can also have short shots (not fully formed parts), warping (distorted parts), jetting (excessive turbulence and air in the part), vacuum voids (air pockets inside the part), and discoloration (bad color variations).
To fix these injection moulding defects, you need to understand the process, materials, and design. By finding and fixing the causes, manufacturers can make better parts, waste less, and meet customer needs.
“Understanding and addressing injection molding defects is crucial for manufacturers to ensure product quality, reduce waste, and optimize production efficiency.”
Conclusion
The injection moulding process is complex but also very versatile. It has its challenges, though. To make high-quality parts, manufacturers must tackle surface defects like dull spots, uneven gloss, and the orange peel effect. By finding out why these defects happen and fixing them, you can make better injection moulded products.
Changing how fast and hot the injection is, improving the mold design, and injecting step by step are key steps. These steps help reduce dull spots, even out the gloss, and get rid of the orange peel effect. This makes your injection moulded parts look better and more consistent.
At THY Precision, we know how important it is to give our clients top-notch injection moulded products. We keep up with the latest in the industry and improve our process step by step. This lets us beat surface defects and make parts that our customers expect. We’re all about making sure your injection moulded parts are perfect and up to your standards.